As the global economy convulses in the post-pandemic landscape, organizations are dealing with a critical conundrum: the pressure to ensure cost-effectiveness in a turbulent market. One significant change we've observed is the strategic shift in supply chain operations from a just-in-case (JIC) stocking strategy to a just-in-time (JIT) model. These economic pressures have made it more crucial than ever for companies to maintain an accurate item master – and with that, comes the importance of operational data matching and how it can optimize JIT supply chain strategies while mitigating the risks associated with incomplete and erroneous data.
Without accurate MRO data, it is difficult to track inventory levels, identify parts that need to be ordered, and ensure that the right parts are delivered to the right place at the right time. This can lead to costly delays, downtime, and even safety hazards.
There are a number of factors that can contribute to poor MRO data quality. These include:
- Duplicate data: This can occur when the same part is entered into the system multiple times with different identifiers (here’s where you might start asking questions about looking for a data matching solution!)
- Incomplete data: This can happen when important information about a part is missing, such as the part number, description, or location.
- Erroneous data: This can occur when incorrect information is entered into the system, such as a wrong part number or description.
The Shift to Just-In-Time MRO
In response to the unprecedented disruptions in the global supply chain during the COVID-19 pandemic, many companies embraced the just-in-case stocking strategy by carrying extra inventory whenever possible. While it was a necessary evil then, the landscape has changed. Now, with the economic pressures of a potential recession and inflation, such stockpiling is often unachievable. The mounting cost of inventory holding along with the cost of good insurance is making the move towards JIT supply chain practices more compelling than ever.
JIT aims to increase efficiency by ordering and receiving goods only when they are needed – helping reduce the cost of holding excess stock. Recessionary pressures, coupled with the escalating costs of stocking products has prompted organizations to reevaluate their approach and adopt JIT supply chain practices, but a successful transition and execution of JIT operations requires precision. Engineers need to be able to easily identify and locate parts they need; and, the purchasing/procurement teams need to have full visibility into expenditures.
The Vital Role of Quality MRO Data
For the JIT approach to supply chain management to be successful, maintaining high-quality Maintenance, Repair, and Operations (MRO) data becomes paramount. Efficient MRO data management helps organizations identify cost-saving opportunities, reduce unnecessary expenditures, and control maintenance expenses which are increasingly burdensome due to inflation.
High-quality MRO data is accurate, complete, and up-to-date. While duplicate data issues can significantly impact MRO data quality, it's essential not to overlook incomplete and erroneous data. Examples of these may include outdated records, inaccurate asset descriptions, and missing documents. Such inaccuracies can lead to price fluctuations, operational efficiency gaps, and inventory deficiencies. Without up-to-date, complete, and easily accessible MRO data, organizations run the risk of incurring excessive costs from order backlogs, delivery delays, and inaccurate orders.
Facing the Costs of Duplicate MRO Data
In the whirlwind of modern business operations, which involve an intricate web of procurement activities across multiple channels and departments, data discrepancies are inevitable. But, this duplicate data can cost companies millions of dollars in unnecessary expenses each year. And truthfully, as the item master becomes more and more polluted with these duplicate records, your equipment downtime and maintenance costs begin to rise, your team can’t locate the necessary parts to get the job done, and false stock-outs occur causing maintenance workers to scramble to expedite parts (spoiler alert: there’s a perfectly good part sitting on the storeroom shelf already, but you can’t locate it within your database because it’s listed under a different description...)
What are the other costs of duplicates? I’m glad you asked:
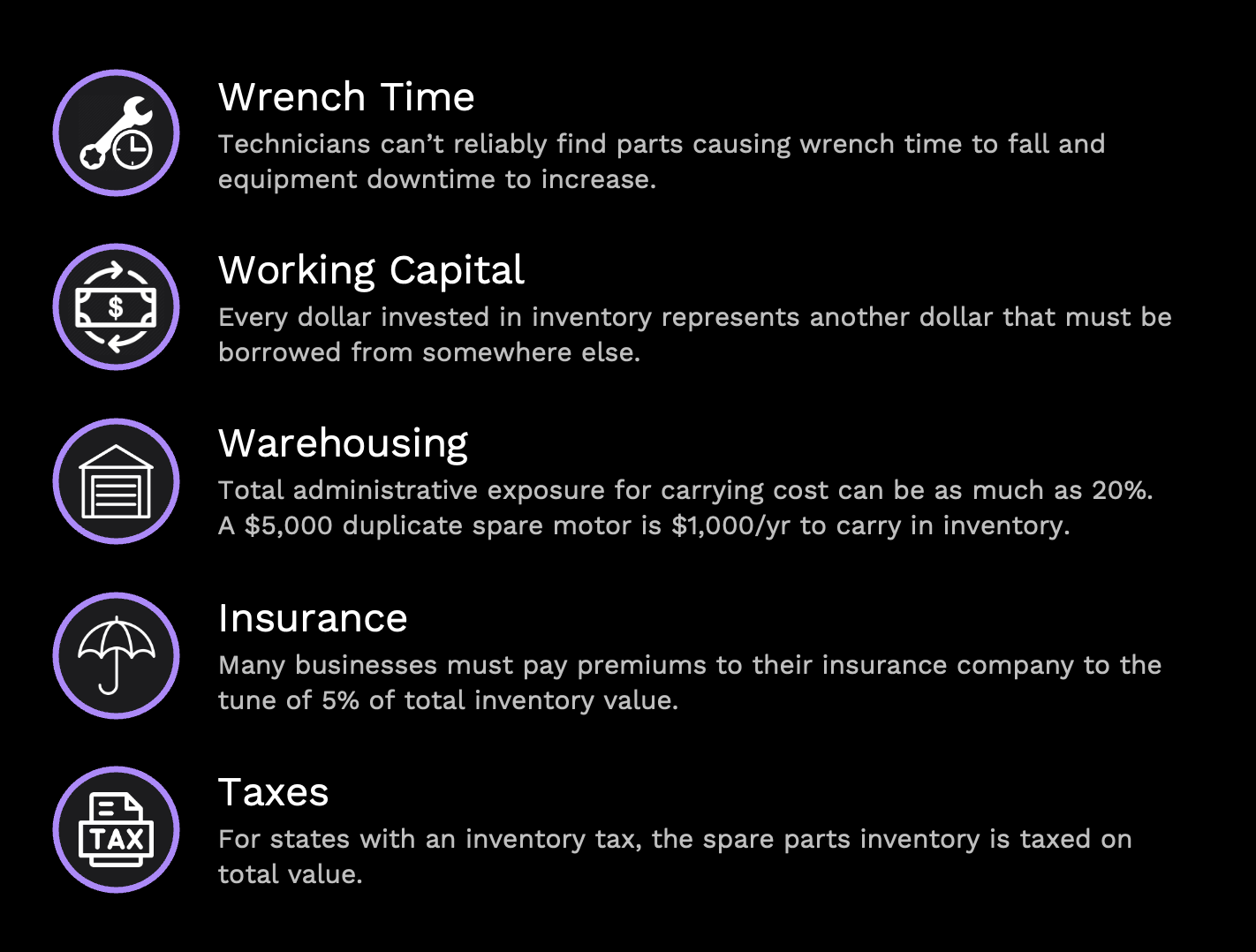
Operational Data Matching as a Solution
Here's where operational data matching comes into play. This process involves linking disparate data sources and identifying inconsistencies to ensure the accuracy and integrity of MRO data. Operational data matching emerges as a powerful solution to tackle the challenges associated with incomplete and erroneous data by employing machine learning algorithms and data analytics to spot and rectify duplicate or incomplete entries, ultimately enhancing the overall quality of MRO data.
By providing a single, reliable source of truth, operational data matching enhances visibility into inventory and expenditure, which are critical for an agile, reliable supply chain. Moreover, it allows for better asset management, resulting in optimized costs and reduced maintenance expenses.
In the face of a volatile economic climate, organizations must be strategic and proactive. With the rising costs of stock holding and the pressure for efficiency, operational data matching can act as a powerful tool in the adoption of JIT supply chain models. Through better MRO data management, we can leverage smart supply chain management to its fullest potential, minimizing costs and enhancing operational efficiency.
Learn more about Syniti Knowledge Platform for MRO here.